Striking by Hand
By around 1279, The Royal Mint sat within the Tower of London. For hundreds of years, English coins were struck by hand; this involved placing a blank piece of metal between a pair of engraved dies and striking it with a hammer. The lower die, known as a pile, had a spiked end driven into a block of wood to hold it firmly in place, whilst a hammer directly hit the upper die, known as a trussel. The trussel wore out faster from the hammer blows, and it carried the reverse design because it was easier to replace than a royal portrait, which usually appeared on the obverse.
Mechanisation
After intermittent trials in the sixteenth century, the minting process in England was finally mechanised in the early 1660s. Metal was cast into fillets that were the same width as and slightly thicker than a coin, reduced by a horse-powered rolling mill, and blanks were punched with a small fly press. Striking took place using a simple screw press, with blanks struck at a rate of one every two seconds. The resulting coins were thicker and vastly superior in quality to those struck by hammer.
Steam Power
In 1810, we left the Tower of London and moved to a new purpose-built facility at nearby Tower Hill which could better accommodate steam-powered machinery. Eight massive presses stood in the Coining Press Room, each capable of striking about 60 coins a minute. In the 1880s, the factory buildings were reconstructed and smaller, faster and quieter machines replaced the presses.
Electrification
At the turn of the twentieth century, steam power gave way to electrification and master tools were increasingly produced using reducing machines. Instead of engraving by hand, at size in steel, an artist could prepare a larger plaster model. A mould was then taken and electroplated with nickel and copper, yielding a reproduction known as an electrotype that could be mounted on an engraving machine and scanned. These movements were communicated to a rotating cutter, which copied them at coin size into a block of steel.
Modern Technology
Since 1968, we have operated from a purpose-built facility in Llantrisant, South Wales. Today, dies created using a digital file are taken from a scan of a plaster model, which is fed into a computer-aided engraving machine. In the Coining Press Room, forklift trucks tip crates of blanks into hoppers, which feed them into the coining press. The dial plate brings each blank to rest on top of the lower die, which moves upwards, pushing the blank into a restraining collar against the upper die with a pressure of around 60 tonnes. A modern coining press can strike up to 850 coins a minute.
Evolution of Coinage Quiz
Discover more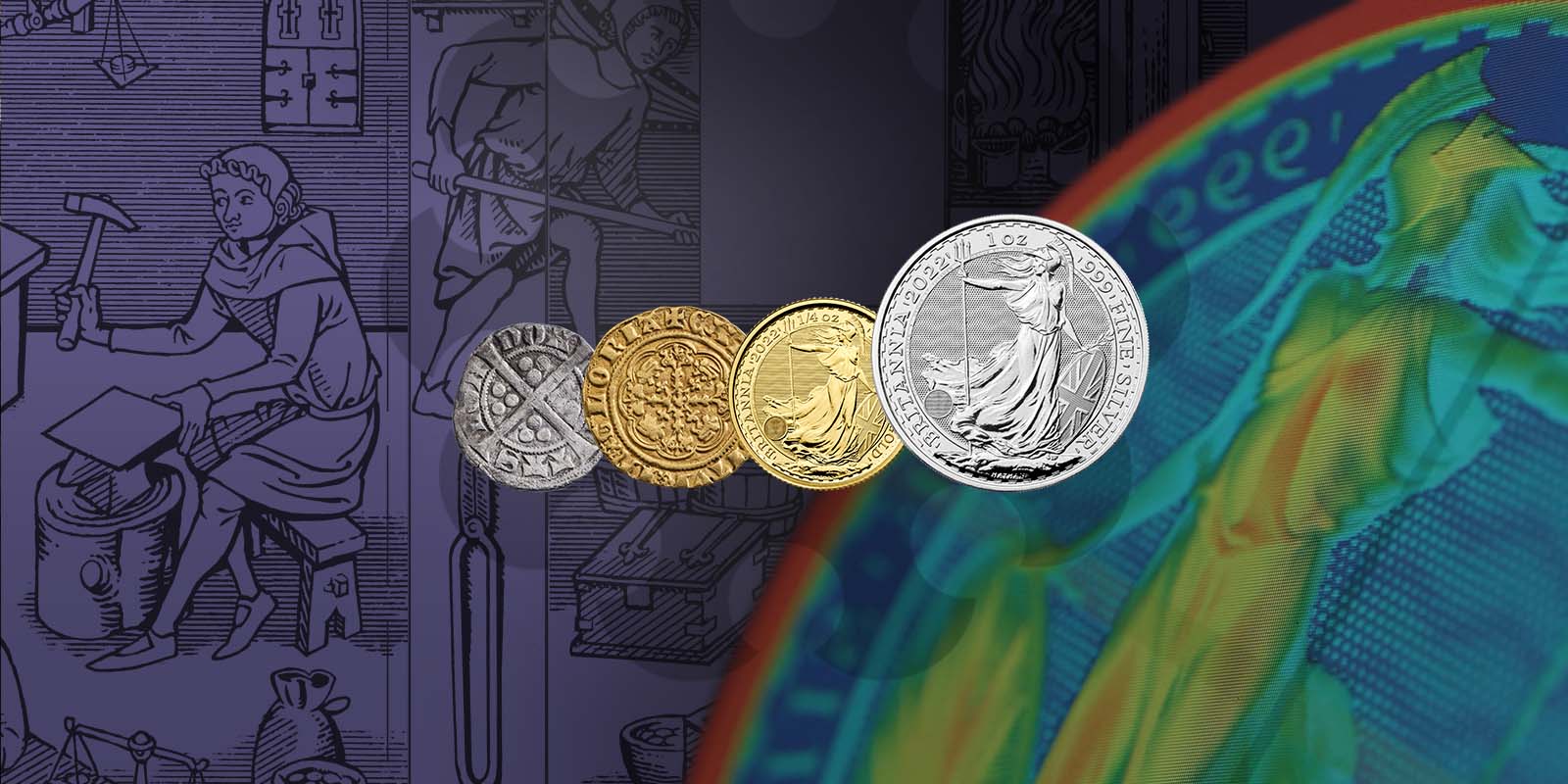